Тэхналогія нарэзкі пласцін, як найважнейшы этап у працэсе вытворчасці паўправаднікоў, непасрэдна звязана з прадукцыйнасцю, выхадам і выдаткамі вытворчасці чыпа.
#01 Перадгісторыя і значэнне нарэзкі вафельных кубікаў
1.1 Вызначэнне нарэзкі вафельных кубікаў
Нарэзка пласцін (таксама вядомая як скрайбінг) — важны этап у вытворчасці паўправаднікоў, накіраваны на падзелу апрацаваных пласцін на некалькі асобных крышталяў. Гэтыя крышталі звычайна ўтрымліваюць поўную функцыянальнасць схемы і з'яўляюцца асноўнымі кампанентамі, якія ў канчатковым выніку выкарыстоўваюцца ў вытворчасці электронных прылад. Па меры таго, як канструкцыі мікрасхем становяцца ўсё больш складанымі, а памеры працягваюць памяншацца, патрабаванні да дакладнасці і эфектыўнасці тэхналогіі нарэзкі пласцін становяцца ўсё больш жорсткімі.
На практыцы для нарэзкі пласцін звычайна выкарыстоўваюцца высокадакладныя інструменты, такія як алмазныя дыскі, каб гарантаваць, што кожны штамп застанецца цэлым і цалкам функцыянальным. Ключавыя этапы ўключаюць падрыхтоўку перад нарэзкай, дакладны кантроль падчас працэсу нарэзкі і кантроль якасці пасля нарэзкі.
Перад разразаннем пласціну неабходна пазначыць і размясціць, каб забяспечыць дакладныя траекторыі разразання. Падчас разразання неабходна строга кантраляваць такія параметры, як ціск інструмента і хуткасць, каб прадухіліць пашкоджанне пласціны. Пасля разразання праводзяцца ўсебаковыя праверкі якасці, каб пераканацца, што кожны чып адпавядае стандартам прадукцыйнасці.
Асноўныя прынцыпы тэхналогіі нарэзкі пласцін ахопліваюць не толькі выбар абсталявання для рэзкі і ўстаноўку параметраў працэсу, але і ўплыў механічных уласцівасцей і характарыстык матэрыялаў на якасць рэзкі. Напрыклад, дыэлектрычныя крэмніевыя пласціны з нізкім утрыманнем дыэлектрыка з-за сваіх горшых механічных уласцівасцей вельмі схільныя да канцэнтрацыі напружанняў падчас рэзкі, што прыводзіць да такіх пашкоджанняў, як сколы і расколіны. Нізкая цвёрдасць і далікатнасць матэрыялаў з нізкім утрыманнем дыэлектрыка робяць іх больш схільнымі да структурных пашкоджанняў пад уздзеяннем механічных сіл або цеплавых нагрузак, асабліва падчас рэзкі. Кантакт паміж інструментам і паверхняй пласціны ў спалучэнні з высокімі тэмпературамі можа яшчэ больш пагоршыць канцэнтрацыю напружанняў.
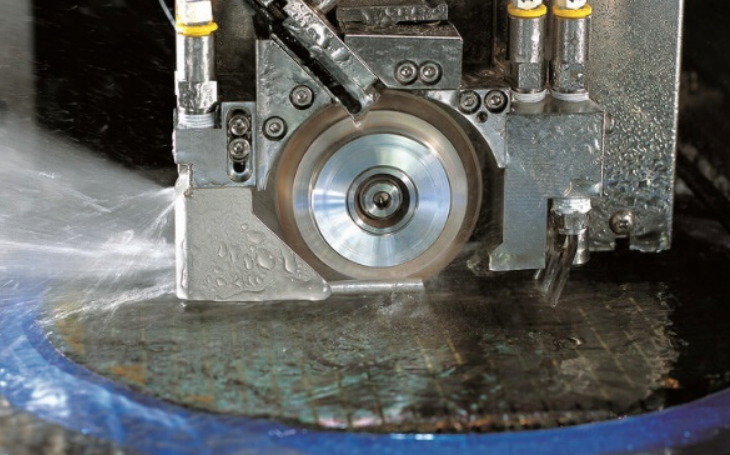
Дзякуючы прагрэсу ў матэрыялазнаўстве, тэхналогія нарэзкі пласцін выйшла за рамкі традыцыйных паўправаднікоў на аснове крэмнію і ўключыла новыя матэрыялы, такія як нітрыд галію (GaN). Гэтыя новыя матэрыялы, дзякуючы сваёй цвёрдасці і структурным уласцівасцям, ствараюць новыя праблемы для працэсаў нарэзкі, патрабуючы далейшага ўдасканалення рэжучых інструментаў і метадаў.
Як найважнейшы працэс у паўправадніковай прамысловасці, высечка пласцін працягвае аптымізаваць у адказ на змяненне патрабаванняў і тэхналагічны прагрэс, закладваючы аснову для будучых тэхналогій мікраэлектронікі і інтэгральных схем.
Паляпшэнні ў тэхналогіі нарэзкі пласцін выходзяць за рамкі распрацоўкі дапаможных матэрыялаў і інструментаў. Яны таксама ахопліваюць аптымізацыю працэсаў, павышэнне прадукцыйнасці абсталявання і дакладны кантроль параметраў нарэзкі. Гэтыя дасягненні накіраваны на забеспячэнне высокай дакладнасці, эфектыўнасці і стабільнасці ў працэсе нарэзкі пласцін, задавальняючы патрэбы паўправадніковай прамысловасці ў меншых памерах, больш высокай інтэграцыі і больш складаных структурах чыпаў.
зона паляпшэння | Канкрэтныя меры | Эфекты |
Аптымізацыя працэсаў | - Паляпшэнне пачатковай падрыхтоўкі, напрыклад, больш дакладнага пазіцыянавання пласцін і планавання шляху. | - Зніжэнне памылак рэзання і паляпшэнне стабільнасці. |
- Мінімізуйце памылкі рэзкі і павысьце стабільнасць. | - Выкарыстоўвайце механізмы маніторынгу і зваротнай сувязі ў рэжыме рэальнага часу для рэгулявання ціску, хуткасці і тэмпературы інструмента. | |
- Зніжэнне ўзроўню паломкі пласцін і паляпшэнне якасці чыпа. | ||
Паляпшэнне прадукцыйнасці абсталявання | - Выкарыстоўваць высокадакладныя механічныя сістэмы і перадавыя тэхналогіі аўтаматызаванага кіравання. | - Павысіць дакладнасць рэзкі і паменшыць страты матэрыялу. |
- Укараненне тэхналогіі лазернай рэзкі, прыдатнай для пласцін з высокацвёрдых матэрыялаў. | - Павысіць эфектыўнасць вытворчасці і скараціць колькасць памылак уручную. | |
- Павысіць аўтаматызацыю абсталявання для аўтаматычнага маніторынгу і рэгулявання. | ||
Дакладны кантроль параметраў | - Дакладная налада параметраў, такіх як глыбіня рэзання, хуткасць, тып інструмента і метады астуджэння. | - Забяспечце цэласнасць крышталя і электрычныя характарыстыкі. |
- Наладзьце параметры ў залежнасці ад матэрыялу пласціны, таўшчыні і структуры. | - Павысіць ураджайнасць, скараціць адходы матэрыялаў і знізіць вытворчыя выдаткі. | |
Стратэгічнае значэнне | - Пастаянна вывучаць новыя тэхналагічныя шляхі, аптымізаваць працэсы і ўдасканальваць магчымасці абсталявання для задавальнення патрэб рынку. | - Паляпшэнне выхаду і прадукцыйнасці вытворчасці мікрасхем, падтрымка распрацоўкі новых матэрыялаў і перадавых канструкцый мікрасхем. |
1.2 Важнасць нарэзкі вафельных кубікаў
Нарэзка пласцін адыгрывае важную ролю ў працэсе вытворчасці паўправаднікоў, непасрэдна ўплываючы на наступныя этапы, а таксама на якасць і прадукцыйнасць канчатковага прадукту. Яе важнасць можна падрабязна апісаць наступным чынам:
Па-першае, дакладнасць і паслядоўнасць нарэзкі з'яўляюцца ключом да забеспячэння выхаду і надзейнасці чыпа. Падчас вытворчасці пласціны праходзяць некалькі этапаў апрацоўкі, каб сфармаваць шматлікія складаныя структуры схем, якія павінны быць дакладна падзелены на асобныя чыпы (крышталі). Калі падчас працэсу нарэзкі ёсць значныя памылкі ў выраўноўванні або нарэзцы, схемы могуць быць пашкоджаны, што паўплывае на функцыянальнасць і надзейнасць чыпа. Такім чынам, тэхналогія высокадакладнай нарэзкі не толькі забяспечвае цэласнасць кожнага чыпа, але і прадухіляе пашкоджанне ўнутраных схем, паляпшаючы агульны ўзровень выхаду.
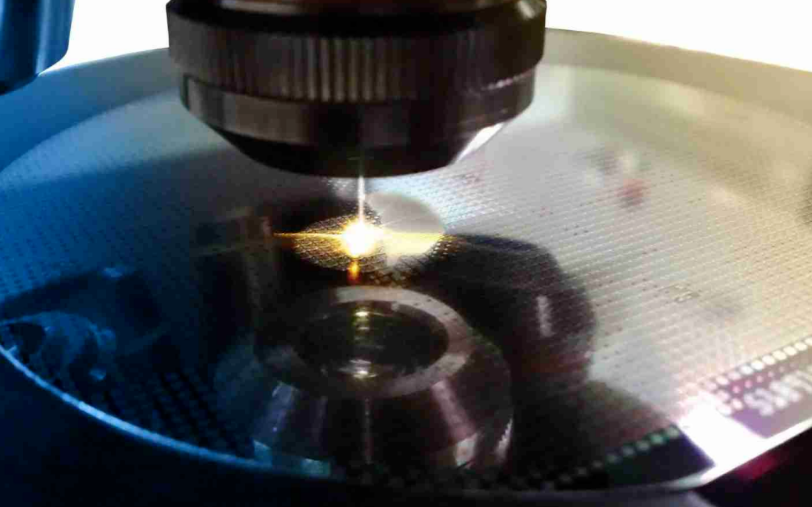
Па-другое, нарэзка пласцін аказвае значны ўплыў на эфектыўнасць вытворчасці і кантроль выдаткаў. Як найважнейшы этап вытворчага працэсу, яго эфектыўнасць непасрэдна ўплывае на ход наступных этапаў. Аптымізацыя працэсу нарэзкі, павышэнне ўзроўню аўтаматызацыі і паляпшэнне хуткасці рэзкі дазваляе значна павысіць агульную эфектыўнасць вытворчасці.
З іншага боку, страты матэрыялу падчас нарэзкі з'яўляюцца крытычна важным фактарам у кіраванні выдаткамі. Выкарыстанне перадавых тэхналогій нарэзкі не толькі памяншае непатрэбныя страты матэрыялу падчас працэсу рэзкі, але і павялічвае выкарыстанне пласцін, тым самым зніжаючы вытворчыя выдаткі.
З развіццём паўправадніковых тэхналогій дыяметр пласцін працягвае павялічвацца, а адпаведна і шчыльнасць схем, што прад'яўляе больш высокія патрабаванні да тэхналогіі нарэзкі. Большыя пласціны патрабуюць больш дакладнага кантролю траекторый рэзкі, асабліва ў зонах высокай шчыльнасці схем, дзе нават нязначныя адхіленні могуць прывесці да дэфектаў некалькіх мікрасхем. Акрамя таго, большыя пласціны ўключаюць больш ліній рэзкі і больш складаныя этапы працэсу, што патрабуе далейшага паляпшэння дакладнасці, паслядоўнасці і эфектыўнасці тэхналогій нарэзкі для вырашэння гэтых праблем.
1.3 Працэс нарэзкі вафельных кубікаў
Працэс нарэзкі вафель кубікамі ахоплівае ўсе этапы, ад падрыхтоўкі да канчатковай праверкі якасці, прычым кожны этап мае вырашальнае значэнне для забеспячэння якасці і прадукцыйнасці нарэзаных чыпсаў. Ніжэй прыведзена падрабязнае тлумачэнне кожнага этапу.
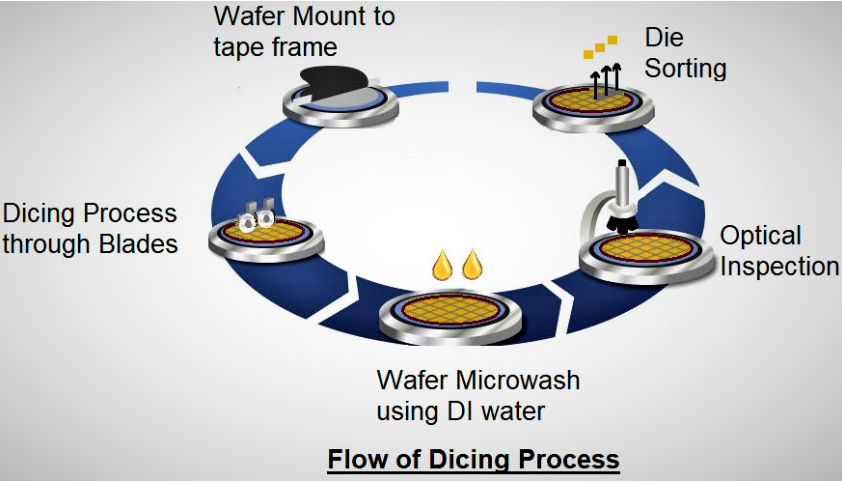
Фаза | Падрабязнае апісанне |
Падрыхтоўчая фаза | -Ачыстка вафельВыкарыстоўвайце высакаякасную ваду і спецыяльныя ачышчальныя сродкі ў спалучэнні з ультрагукавой або механічнай ачысткай для выдалення прымешак, часціц і забруджванняў, забяспечваючы чыстую паверхню. -Дакладнае пазіцыянаваннеВыкарыстоўвайце высокадакладнае абсталяванне, каб забяспечыць дакладнае падзеленне пласціны па распрацаваных шляхах рэзкі. -Фіксацыя вафельЗамацуйце пласціну на стужцы-рамцы, каб забяспечыць стабільнасць падчас рэзкі і прадухіліць пашкоджанне ад вібрацыі або руху. |
Этап рэзкі | -Нарэзка кубікамі лязаВыкарыстоўвайце для фізічнай рэзкі высакахуткасныя круцільныя ляза з алмазным пакрыццём, якія падыходзяць для матэрыялаў на аснове крэмнію і з'яўляюцца эканамічна выгаднымі. -Лазерная нарэзка кубікаміВыкарыстоўвайце высокаэнергетычныя лазерныя прамяні для бескантактавай рэзкі, ідэальна падыходзяць для далікатных або высокацвёрдых матэрыялаў, такіх як нітрыд галію, забяспечваючы больш высокую дакладнасць і меншыя страты матэрыялу. -Новыя тэхналогііУкараненне тэхналогій лазернай і плазменнай рэзкі для далейшага павышэння эфектыўнасці і дакладнасці пры адначасовым мінімізацыі зон цеплавога ўздзеяння. |
Этап ачысткі | - Выкарыстоўвайце дэіянізаваную ваду (DE-ваду) і спецыяльныя ачышчальныя сродкі ў спалучэнні з ультрагукавой або распыляльнай ачысткай для выдалення смецця і пылу, якія ўтвараюцца падчас рэзкі, прадухіляючы ўплыў рэшткаў на наступныя працэсы або электрычныя характарыстыкі стружкі. - Высокачышчаная дэіеляваная вада прадухіляе ўнясенне новых забруджвальнікаў, забяспечваючы чыстае асяроддзе для пласцін. |
Этап праверкі | -Аптычны аглядВыкарыстоўвайце аптычныя сістэмы выяўлення ў спалучэнні з алгарытмамі штучнага інтэлекту для хуткага выяўлення дэфектаў, гарантуючы адсутнасць расколін або сколаў у нарэзанай стружцы, павышаючы эфектыўнасць кантролю і змяншаючы колькасць памылак чалавека. -Вымярэнне памераўПраверце, ці адпавядаюць памеры чыпа праектным патрабаванням. -Выпрабаванні электрычных характарыстыкЗабяспечваць адпаведнасць электрычных характарыстык крытычна важных мікрасхем стандартам, што гарантуе надзейнасць у наступных ужываннях. |
Этап сартавання | - Выкарыстоўвайце рабатызаваныя рукі або вакуумныя прысоскі для аддзялення кваліфікаваных чыпаў ад рамы стужкі і аўтаматычнай сартавання іх у залежнасці ад прадукцыйнасці, забяспечваючы эфектыўнасць і гнуткасць вытворчасці, адначасова павышаючы дакладнасць. |
Працэс рэзкі пласцін уключае ачыстку, пазіцыянаванне, разразанне, ачыстку, праверку і сартаванне пласцін, прычым кожны этап мае вырашальнае значэнне. Дзякуючы развіццю тэхналогій аўтаматызацыі, лазернай рэзкі і інспекцыі з дапамогай штучнага інтэлекту, сучасныя сістэмы рэзкі пласцін могуць дасягнуць больш высокай дакладнасці, хуткасці і меншых страт матэрыялу. У будучыні новыя тэхналогіі рэзкі, такія як лазерная і плазменная, паступова заменяць традыцыйную рэзку лязамі, каб задаволіць патрэбы ўсё больш складаных канструкцый мікрасхем, што будзе яшчэ больш стымуляваць развіццё працэсаў вытворчасці паўправаднікоў.
Тэхналогія рэзкі вафель і яе прынцыпы
На малюнку паказаны тры распаўсюджаныя тэхналогіі рэзкі пласцін:Нарэзка кубікамі ляза,Лазерная нарэзка кубікамііПлазменная нарэзка кубікаміНіжэй прыведзены падрабязны аналіз і дадатковае тлумачэнне гэтых трох метадаў:
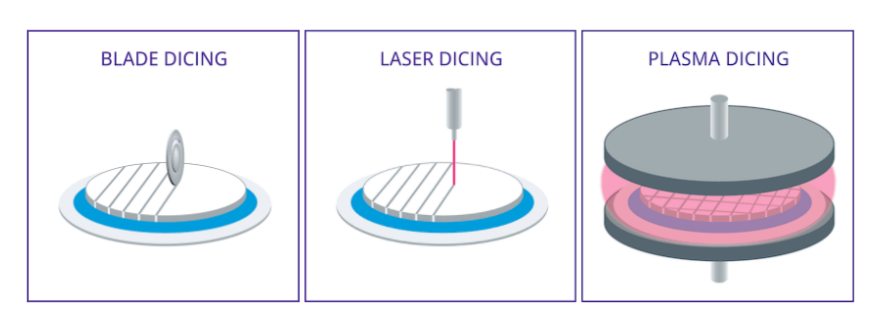
У вытворчасці паўправаднікоў рэзка пласцін з'яўляецца найважнейшым этапам, які патрабуе выбару адпаведнага метаду рэзкі ў залежнасці ад таўшчыні пласціны. Першы крок - вызначыць таўшчыню пласціны. Калі таўшчыня пласціны перавышае 100 мікрон, у якасці метаду рэзкі можна выбраць нарэзку лязом. Калі нарэзка лязом не падыходзіць, можна выкарыстоўваць метад нарэзкі з разломам, які ўключае ў сябе як тэхніку надрэзкі, так і нарэзкі лязом.
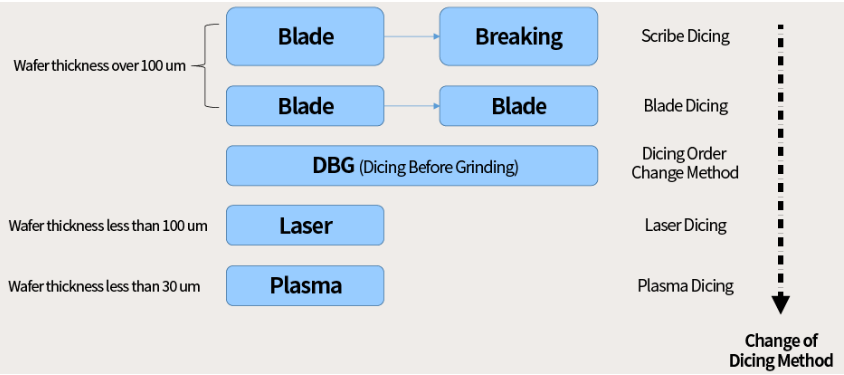
Калі таўшчыня пласціны складае ад 30 да 100 мікрон, рэкамендуецца метад DBG (Dice Before Grinding). У гэтым выпадку для дасягнення найлепшых вынікаў можна выбраць разрэзку па шкале, нарэзку кубікамі лязом або карэкціроўку паслядоўнасці рэзкі па меры неабходнасці.
Для ультратонкіх пласцін таўшчынёй менш за 30 мікрон лазерная рэзка становіцца пераважным метадам дзякуючы яго здольнасці дакладна рэзаць тонкія пласціны без празмерных пашкоджанняў. Калі лазерная рэзка не можа задаволіць пэўныя патрабаванні, у якасці альтэрнатывы можна выкарыстоўваць плазменную рэзку. Гэтая блок-схема забяспечвае выразны шлях прыняцця рашэнняў, каб гарантаваць выбар найбольш прыдатнай тэхналогіі рэзкі пласцін пры розных умовах таўшчыні.
2.1 Тэхналогія механічнага рэзання
Тэхналогія механічнай рэзкі — гэта традыцыйны метад нарэзкі пласцін. Асноўны прынцып заключаецца ў выкарыстанні хуткаснага кручэння алмазнага шліфавальнага круга ў якасці рэжучага інструмента для нарэзкі пласціны. Асноўнае абсталяванне ўключае шпіндзель з пнеўматычным падшыпнікам, які прыводзіць у рух алмазны шліфавальны круг з высокай хуткасцю для выканання дакладнай рэзкі або нанясення канавок па зададзенай траекторыі рэзкі. Гэтая тэхналогія шырока выкарыстоўваецца ў прамысловасці дзякуючы нізкай кошту, высокай эфектыўнасці і шырокаму прымяненню.
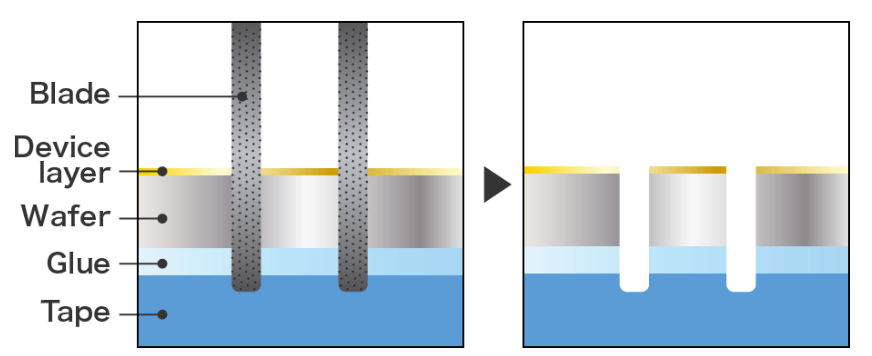
Перавагі
Высокая цвёрдасць і зносаўстойлівасць алмазных шліфавальных кругоў дазваляюць адаптаваць тэхналогію механічнай рэзкі да патрэб рэзання розных матэрыялаў пласцін, няхай гэта будзе традыцыйныя матэрыялы на аснове крэмнію або новыя злучэнні паўправаднікоў. Іх эксплуатацыя простая, з адносна нізкімі тэхнічнымі патрабаваннямі, што яшчэ больш спрыяе іх папулярнасці ў масавай вытворчасці. Акрамя таго, у параўнанні з іншымі метадамі рэзкі, такімі як лазерная рэзка, механічная рэзка мае больш кантраляваныя выдаткі, што робіць яе прыдатнай для патрэб масавай вытворчасці.
Абмежаванні
Нягледзячы на шматлікія перавагі, тэхналогія механічнай рэзкі мае і абмежаванні. Па-першае, з-за фізічнага кантакту паміж інструментам і пласцінай дакладнасць рэзкі адносна абмежаваная, што часта прыводзіць да адхіленняў памераў, якія могуць паўплываць на дакладнасць наступнай упакоўкі і выпрабаванняў чыпаў. Па-другое, падчас працэсу механічнай рэзкі могуць лёгка ўзнікнуць такія дэфекты, як сколы і расколіны, што не толькі ўплывае на хуткасць выхаду, але і можа негатыўна адбіцца на надзейнасці і тэрміне службы чыпаў. Пашкоджанні, выкліканыя механічным напружаннем, асабліва негатыўныя для вытворчасці чыпаў высокай шчыльнасці, асабліва пры рэзанні далікатных матэрыялаў, дзе гэтыя праблемы больш выяўленыя.
Тэхналагічныя ўдасканаленні
Каб пераадолець гэтыя абмежаванні, даследчыкі пастаянна аптымізуюць працэс механічнага рэзання. Ключавыя паляпшэнні ўключаюць удасканаленне канструкцыі і выбару матэрыялаў шліфавальных колаў для павышэння дакладнасці і даўгавечнасці рэзання. Акрамя таго, аптымізацыя канструкцыйнага праектавання і сістэм кіравання рэжучым абсталяваннем яшчэ больш палепшыла стабільнасць і аўтаматызацыю працэсу рэзання. Гэтыя дасягненні памяншаюць памылкі, выкліканыя чалавечымі дзеяннямі, і паляпшаюць кансістэнцыю рэзання. Укараненне перадавых тэхналогій кантролю і кантролю якасці для маніторынгу анамалій у рэжыме рэальнага часу падчас працэсу рэзання таксама значна павысіла надзейнасць рэзання і прыбытак.
Будучае развіццё і новыя тэхналогіі
Нягледзячы на тое, што тэхналогія механічнай рэзкі ўсё яшчэ займае значнае месца ў рэзанні пласцін, новыя тэхналогіі рэзкі хутка развіваюцца па меры развіцця паўправадніковых працэсаў. Напрыклад, прымяненне тэхналогіі тэрмічнай лазернай рэзкі прапануе новыя рашэнні для праблем дакладнасці і дэфектаў пры механічнай рэзцы. Гэты бескантактавы метад рэзкі змяншае фізічную нагрузку на пласціну, значна зніжаючы частату сколаў і расколін, асабліва пры рэзанні больш далікатных матэрыялаў. У будучыні інтэграцыя тэхналогіі механічнай рэзкі з новымі метадамі рэзкі забяспечыць вытворчасць паўправаднікоў большымі магчымасцямі і гнуткасцю, што яшчэ больш павысіць эфектыўнасць вытворчасці і якасць чыпаў.
У заключэнне, хоць тэхналогія механічнай рэзкі мае пэўныя недахопы, пастаянныя тэхналагічныя ўдасканаленні і яе інтэграцыя з новымі метадамі рэзкі дазваляюць ёй працягваць гуляць важную ролю ў вытворчасці паўправаднікоў і падтрымліваць сваю канкурэнтаздольнасць у будучых працэсах.
2.2 Тэхналогія лазернай рэзкі
Тэхналогія лазернай рэзкі, як новы метад рэзкі пласцін, паступова прыцягнула шырокую ўвагу ў паўправадніковай прамысловасці дзякуючы высокай дакладнасці, адсутнасці механічных кантактных пашкоджанняў і хуткай рэзцы. Гэтая тэхналогія выкарыстоўвае высокую шчыльнасць энергіі і факусуючую здольнасць лазернага прамяня для стварэння невялікай зоны цеплавога ўздзеяння на паверхні матэрыялу пласціны. Калі лазерны прамень прыкладваецца да пласціны, узнікае цеплавое напружанне, якое ўзнікае, прыводзіць да разлому матэрыялу ў патрэбным месцы, што дазваляе дасягнуць дакладнай рэзкі.
Перавагі тэхналогіі лазернай рэзкі
• Высокая дакладнасцьДакладнае пазіцыянаванне лазернага прамяня дазваляе рэзаць з дакладнасцю да мікроннага або нават нанаметравага ўзроўню, што адпавядае патрабаванням сучаснай вытворчасці высокадакладных інтэгральных схем высокай шчыльнасці.
• Няма механічнага кантактуЛазерная рэзка дазваляе пазбегнуць фізічнага кантакту з пласцінай, прадухіляючы распаўсюджаныя праблемы механічнай рэзкі, такія як сколы і расколіны, значна паляпшаючы выхад і надзейнасць чыпаў.
• Высокая хуткасць рэзкіВысокая хуткасць лазернай рэзкі спрыяе павышэнню эфектыўнасці вытворчасці, што робіць яе асабліва прыдатнай для маштабных вытворчых сцэнарыяў з высокай хуткасцю.
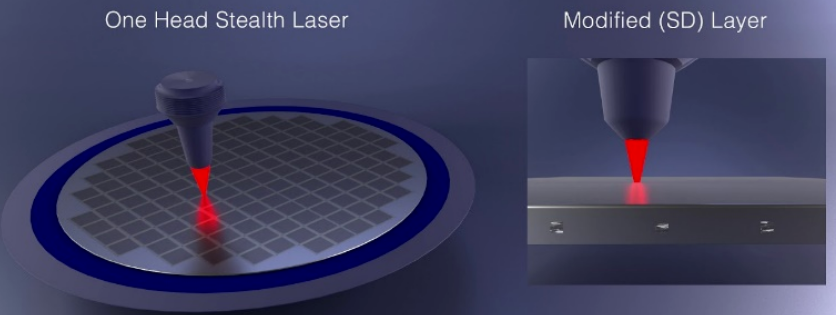
Сутыкнуліся з праблемамі
• Высокі кошт абсталяванняПачатковыя інвестыцыі ў абсталяванне для лазернай рэзкі высокія, што стварае эканамічны ціск, асабліва для малых і сярэдніх вытворчых прадпрыемстваў.
• Комплекснае кіраванне працэсаміЛазерная рэзка патрабуе дакладнага кантролю некалькіх параметраў, у тым ліку шчыльнасці энергіі, становішча фокусу і хуткасці рэзання, што робіць працэс складаным.
• Праблемы з зонай, якая падвяргаецца ўздзеянню цяплаНягледзячы на тое, што бескантактавы характар лазернай рэзкі памяншае механічныя пашкоджанні, цеплавое напружанне, выкліканае зонай цеплавога ўздзеяння (ЗТВ), можа негатыўна паўплываць на ўласцівасці матэрыялу пласціны. Для мінімізацыі гэтага эфекту неабходная далейшая аптымізацыя працэсу.
Кірункі тэхналагічнага ўдасканалення
Каб вырашыць гэтыя праблемы, даследчыкі засяроджваюцца на зніжэнні выдаткаў на абсталяванне, павышэнні эфектыўнасці рэзкі і аптымізацыі тэхналагічнага працэсу.
• Эфектыўныя лазеры і аптычныя сістэмыРаспрацоўваючы больш эфектыўныя лазеры і перадавыя аптычныя сістэмы, можна знізіць выдаткі на абсталяванне, адначасова павышаючы дакладнасць і хуткасць рэзкі.
• Аптымізацыя параметраў працэсуПраводзяцца паглыбленыя даследаванні ўзаемадзеяння паміж лазерамі і пласціннымі матэрыяламі з мэтай удасканалення працэсаў, якія памяншаюць зону цеплавога ўздзеяння, тым самым паляпшаючы якасць рэзкі.
• Інтэлектуальныя сістэмы кіраванняРаспрацоўка інтэлектуальных тэхналогій кіравання накіравана на аўтаматызацыю і аптымізацыю працэсу лазернай рэзкі, паляпшэнне яго стабільнасці і паслядоўнасці.
Тэхналогія лазернай рэзкі асабліва эфектыўная ў выпадку звыштонкіх пласцін і высокадакладнай рэзкі. Па меры павелічэння памераў пласцін і павелічэння шчыльнасці схем традыцыйныя метады механічнай рэзкі з цяжкасцю спраўляюцца з патрабаваннямі да высокай дакладнасці і эфектыўнасці сучаснай вытворчасці паўправаднікоў. Дзякуючы сваім унікальным перавагам, лазерная рэзка становіцца пераважным рашэннем у гэтых галінах.
Нягледзячы на тое, што тэхналогія лазернай рэзкі ўсё яшчэ сутыкаецца з такімі праблемамі, як высокі кошт абсталявання і складанасць працэсу, яе ўнікальныя перавагі ў высокай дакладнасці і бескантактавым пашкоджанні робяць яе важным напрамкам развіцця ў вытворчасці паўправаднікоў. Па меры далейшага развіцця лазерных тэхналогій і інтэлектуальных сістэм кіравання чакаецца, што лазерная рэзка яшчэ больш палепшыць эфектыўнасць і якасць рэзкі пласцін, што будзе стымуляваць пастаяннае развіццё паўправадніковай прамысловасці.
2.3 Тэхналогія плазменнай рэзкі
Тэхналогія плазменнай рэзкі, як новы метад нарэзкі пласцін, прыцягнула значную ўвагу ў апошнія гады. Гэтая тэхналогія выкарыстоўвае высокаэнергетычныя плазменныя прамяні для дакладнай рэзкі пласцін, кантралюючы энергію, хуткасць і шлях рэзкі плазменнага прамяня, дасягаючы аптымальных вынікаў рэзкі.
Прынцып працы і перавагі
Працэс плазменнай рэзкі заснаваны на высокатэмпературным і высокаэнергетычным плазменным пучку, які генеруецца абсталяваннем. Гэты прамень можа нагрэць матэрыял пласціны да кропкі плаўлення або выпарэння за вельмі кароткі прамежак часу, што дазваляе хутка рэзаць. У параўнанні з традыцыйнай механічнай або лазернай рэзкай, плазменная рэзка хутчэйшая і стварае меншую зону цеплавога ўздзеяння, што эфектыўна памяншае ўзнікненне расколін і пашкоджанняў падчас рэзкі.
У практычным ужыванні тэхналогія плазменнай рэзкі асабліва добра падыходзіць для апрацоўкі пласцін складанай формы. Яе высокаэнергетычны рэгуляваны плазменны прамень можа лёгка рэзаць пласціны няправільнай формы з высокай дакладнасцю. Такім чынам, у вытворчасці мікраэлектронікі, асабліва ў вытворчасці высакаякасных мікрасхем на заказ і дробнымі партыямі, гэтая тэхналогія мае вялікія перспектывы для шырокага выкарыстання.
Праблемы і абмежаванні
Нягледзячы на шматлікія перавагі тэхналогіі плазменнай рэзкі, яна таксама сутыкаецца з некаторымі праблемамі.
• Складаны працэсПрацэс плазменнай рэзкі складаны і патрабуе высокадакладнага абсталявання і вопытных аператараў.дакладнасць і стабільнасць пры рэзанні.
• Кантроль навакольнага асяроддзя і бяспекаВысокатэмпературная і высокаэнергетычная прырода плазменнага пучка патрабуе строгага кантролю за ўздзеяннем навакольнага асяроддзя і мер бяспекі, што павялічвае складанасць і кошт рэалізацыі.
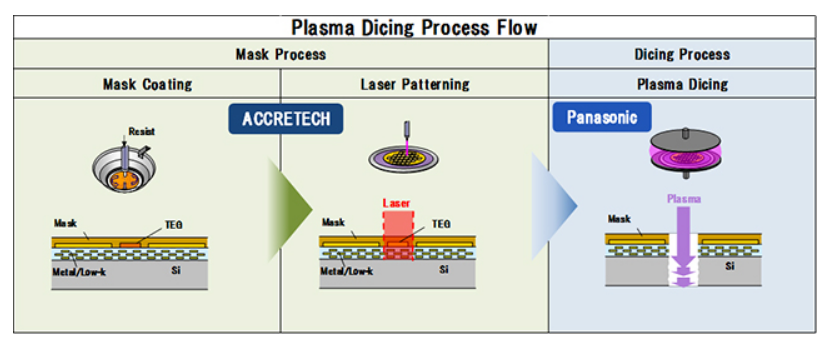
Напрамкі развіцця будучыні
Чакаецца, што з развіццём тэхналогій праблемы, звязаныя з плазменнай рэзкай, будуць паступова пераадолены. Распрацоўка больш разумнага і стабільнага абсталявання для рэзкі дазваляе знізіць залежнасць ад ручнога выкананні аперацый, тым самым павышаючы эфектыўнасць вытворчасці. Адначасова аптымізацыя параметраў працэсу і асяроддзя рэзкі дапаможа знізіць рызыкі бяспекі і эксплуатацыйныя выдаткі.
У паўправадніковай прамысловасці інавацыі ў тэхналогіі рэзкі і нарэзкі пласцін маюць вырашальнае значэнне для развіцця галіны. Тэхналогія плазменнай рэзкі, якая адрозніваецца высокай дакладнасцю, эфектыўнасцю і здольнасцю апрацоўваць пласціны складанай формы, стала новым значным гульцом у гэтай галіне. Нягледзячы на тое, што некаторыя праблемы застаюцца, яны будуць паступова вырашацца з дапамогай бесперапынных тэхналагічных інавацый, што адкрые больш магчымасцей для вытворчасці паўправаднікоў.
Перспектывы прымянення тэхналогіі плазменнай рэзкі велізарныя, і чакаецца, што ў будучыні яна будзе адыгрываць больш важную ролю ў вытворчасці паўправаднікоў. Дзякуючы пастаянным тэхналагічным інавацыям і аптымізацыі плазменная рэзка не толькі вырашыць існуючыя праблемы, але і стане магутным рухавіком росту паўправадніковай прамысловасці.
2.4 Якасць рэзкі і фактары ўплыву
Якасць рэзкі пласцін мае вырашальнае значэнне для наступнай упакоўкі чыпаў, выпрабаванняў, а таксама для агульнай прадукцыйнасці і надзейнасці канчатковага прадукту. Да распаўсюджаных праблем, якія ўзнікаюць падчас рэзкі, адносяцца расколіны, сколы і адхіленні ад рэзкі. На гэтыя праблемы ўплывае некалькі фактараў, якія ўздзейнічаюць разам.
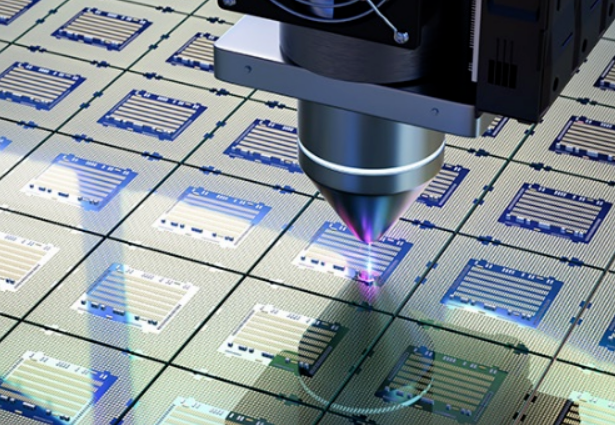
Катэгорыя | Змест | Уплыў |
Параметры працэсу | Хуткасць рэзання, падача і глыбіня рэзання непасрэдна ўплываюць на стабільнасць і дакладнасць працэсу рэзання. Няправільныя налады могуць прывесці да канцэнтрацыі напружанняў і празмернай зоны цеплавога ўздзеяння, што ў выніку прывядзе да расколін і сколаў. Адпаведная карэкціроўка параметраў у залежнасці ад матэрыялу пласціны, таўшчыні і патрабаванняў да рэзання з'яўляецца ключом да дасягнення жаданых вынікаў рэзання. | Правільныя параметры працэсу забяспечваюць дакладную рэзку і зніжаюць рызыку дэфектаў, такіх як расколіны і сколы. |
Фактары абсталявання і матэрыялаў | -Якасць лязаМатэрыял, цвёрдасць і зносаўстойлівасць ляза ўплываюць на плаўнасць працэсу рэзання і роўнасць паверхні рэзання. Няякасныя ляза павялічваюць трэнне і цеплавое напружанне, што можа прывесці да расколін або сколаў. Выбар правільнага матэрыялу ляза мае вырашальнае значэнне. -Прадукцыйнасць астуджальнай вадкасціАстуджальныя вадкасці дапамагаюць знізіць тэмпературу рэзання, мінімізаваць трэнне і выдаляць смецце. Неэфектыўная астуджальная вадкасць можа прывесці да высокіх тэмператур і назапашвання смецця, што ўплывае на якасць і эфектыўнасць рэзання. Выбар эфектыўных і экалагічна чыстых астуджальных вадкасцей мае жыццёва важнае значэнне. | Якасць ляза ўплывае на дакладнасць і гладкасць рэзу. Неэфектыўная астуджальная вадкасць можа прывесці да нізкай якасці рэзу і эфектыўнасці, што падкрэслівае неабходнасць аптымальнага выкарыстання астуджальнай вадкасці. |
Кантроль працэсаў і кантроль якасці | -Кантроль працэсаўМаніторынг і карэкціроўка ключавых параметраў рэзання ў рэжыме рэальнага часу для забеспячэння стабільнасці і паслядоўнасці працэсу рэзання. -Кантроль якасціПраверка знешняга выгляду пасля рэзкі, вымярэнне памераў і выпрабаванні электрычных характарыстык дапамагаюць своечасова выяўляць і вырашаць праблемы з якасцю, паляпшаючы дакладнасць і стабільнасць рэзкі. | Правільны кантроль працэсу і праверка якасці дапамагаюць забяспечыць стабільныя, высакаякасныя вынікі рэзкі і ранняе выяўленне патэнцыйных праблем. |

Паляпшэнне якасці рэзкі
Паляпшэнне якасці рэзкі патрабуе комплекснага падыходу, які ўлічвае параметры працэсу, выбар абсталявання і матэрыялаў, кантроль працэсу і кантроль. Дзякуючы пастаяннаму ўдасканаленню тэхналогій рэзкі і аптымізацыі метадаў працэсу, можна яшчэ больш павысіць дакладнасць і стабільнасць рэзкі пласцін, забяспечваючы больш надзейную тэхнічную падтрымку для паўправадніковай прамысловасці.
#03 Апрацоўка і выпрабаванні пасля рэзкі
3.1 Чыстка і сушка
Этапы ачысткі і сушкі пасля рэзкі пласціны маюць вырашальнае значэнне для забеспячэння якасці чыпа і бесперабойнага праходжання наступных працэсаў. На гэтым этапе важна старанна выдаліць рэшткі крэмнію, рэшткі астуджальнай вадкасці і іншыя забруджванні, якія ўтвараюцца падчас рэзкі. Гэтак жа важна сачыць за тым, каб чып не быў пашкоджаны падчас працэсу ачысткі, а пасля сушкі пераканацца, што на паверхні чыпа не засталося вільгаці, каб прадухіліць такія праблемы, як карозія або электрастатычны разрад.
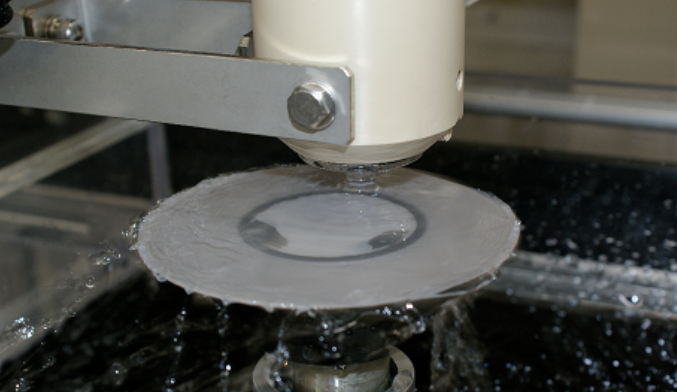
Апрацоўка пасля рэзкі: працэс ачысткі і сушкі
Этап працэсу | Змест | Уплыў |
Працэс ачысткі | -МетадВыкарыстоўвайце спецыялізаваныя ачышчальныя сродкі і чыстую ваду ў спалучэнні з ультрагукавымі або механічнымі метадамі ачысткі. | Забяспечвае дбайнае выдаленне забруджванняў і прадухіляе пашкоджанне стружкі падчас чысткі. |
-Выбар ачышчальнага сродкуВыбірайце ў залежнасці ад матэрыялу пласціны і тыпу забруджвання, каб забяспечыць эфектыўную ачыстку без пашкоджання чыпа. | Правільны выбар сродку з'яўляецца ключом да эфектыўнай ачысткі і абароны ад сколаў. | |
-Кіраванне параметраміСтрога кантралюйце тэмпературу, час і канцэнтрацыю ачышчальнага раствора, каб прадухіліць праблемы з якасцю, выкліканыя няправільнай ачысткай. | Кантроль дапамагае пазбегнуць пашкоджання пласціны або забруджванняў, забяспечваючы стабільную якасць. | |
Працэс сушкі | -Традыцыйныя метадыНатуральнае паветранае сушэнне і сушка гарачым паветрам, якія маюць нізкую эфектыўнасць і могуць прывесці да назапашвання статычнай электрычнасці. | Гэта можа прывесці да павольнага часу высыхання і магчымых праблем са статычнай электрычнасцю. |
-Сучасныя тэхналогііВыкарыстоўвайце перадавыя тэхналогіі, такія як вакуумная сушка і інфрачырвоная сушка, каб забяспечыць хуткае высыханне чыпсаў і пазбегнуць шкодных наступстваў. | Хутчэйшы і больш эфектыўны працэс сушкі, што зніжае рызыку статычнага разраду або праблем, звязаных з вільгаццю. | |
Выбар абсталявання і абслугоўванне | -Выбар абсталяванняВысокапрадукцыйныя машыны для ачысткі і сушкі павышаюць эфектыўнасць апрацоўкі і дакладна кантралююць патэнцыйныя праблемы падчас апрацоўкі. | Высокаякасныя машыны забяспечваюць лепшую апрацоўку і зніжаюць верагоднасць памылак падчас чысткі і сушкі. |
-Тэхнічнае абслугоўванне абсталяванняРэгулярны агляд і тэхнічнае абслугоўванне абсталявання забяспечваюць яго аптымальны працоўны стан, гарантуючы якасць стружкі. | Належнае тэхнічнае абслугоўванне прадухіляе паломкі абсталявання, забяспечваючы надзейную і якасную апрацоўку. |
Ачыстка і сушка пасля рэзкі
Этапы ачысткі і сушкі пасля разразання пласцін — гэта складаныя і далікатныя працэсы, якія патрабуюць уважлівага ўліку мноства фактараў для забеспячэння канчатковага выніку апрацоўкі. Выкарыстоўваючы навуковыя метады і строгія працэдуры, можна гарантаваць, што кожны чып паступае на наступныя этапы ўпакоўкі і тэсціравання ў аптымальным стане.
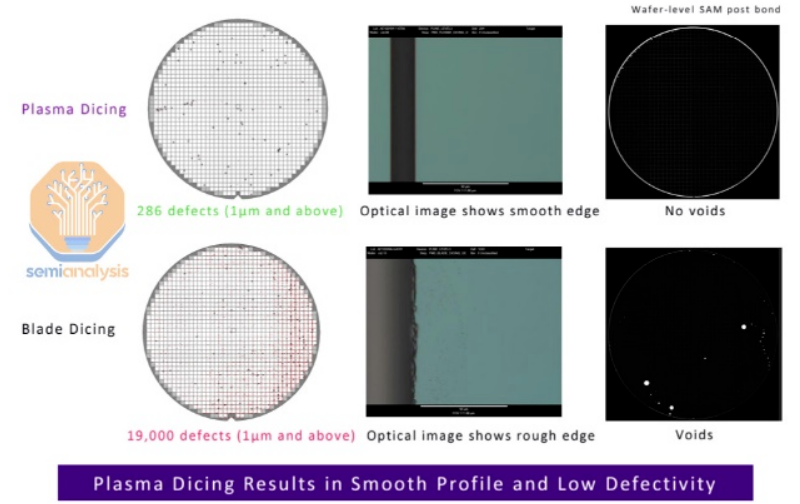
Кантроль і выпрабаванні пасля рэзкі
Крок | Змест | Уплыў |
Этап праверкі | 1.Візуальны аглядВыкарыстоўвайце візуальнае або аўтаматызаванае абсталяванне для праверкі на наяўнасць бачных дэфектаў, такіх як расколіны, сколы або забруджванне на паверхні стружкі. Хутка выяўляйце фізічна пашкоджаную стружку, каб пазбегнуць адходаў. | Дапамагае выяўляць і ліквідаваць дэфектныя стружкі на ранніх этапах працэсу, памяншаючы страты матэрыялу. |
2.Вымярэнне памеруВыкарыстоўвайце дакладныя вымяральныя прылады для дакладнага вымярэння памераў чыпсаў, гарантуючы, што памер рэзкі адпавядае канструктыўным патрабаванням і прадухіляе праблемы з прадукцыйнасцю або цяжкасці з упакоўкай. | Забяспечвае адпаведнасць памераў чыпаў патрабаваным абмежаванням, прадухіляючы зніжэнне прадукцыйнасці або праблемы са зборкай. | |
3.Выпрабаванні электрычных характарыстыкАцаніце ключавыя электрычныя параметры, такія як супраціўленне, ёмістасць і індуктыўнасць, каб выявіць неадпаведныя мікрасхемы і гарантаваць, што да наступнага этапу будуць пераходзіць толькі тыя мікрасхемы, якія адпавядаюць патрабаванням. | Забяспечвае выкарыстанне толькі функцыянальных і правераных на прадукцыйнасць мікрасхем, што зніжае рызыку збою на пазнейшых этапах. | |
Этап тэставання | 1.Функцыянальнае тэставаннеПраверка таго, што асноўная функцыянальнасць чыпа працуе належным чынам, выяўленне і выдаленне чыпаў з функцыянальнымі парушэннямі. | Забяспечвае адпаведнасць чыпаў асноўным эксплуатацыйным патрабаванням, перш чым пераходзіць да наступных этапаў. |
2.Тэставанне надзейнасціАцэнка стабільнасці прадукцыйнасці чыпа пры працяглым выкарыстанні або ў жорсткіх умовах, звычайна з выкарыстаннем высокатэмпературнага старэння, нізкатэмпературных выпрабаванняў і выпрабаванняў на вільготнасць для імітацыі рэальных экстрэмальных умоў. | Забяспечвае надзейную працу мікрасхем у розных умовах навакольнага асяроддзя, павялічваючы тэрмін службы і стабільнасць прадукту. | |
3.Тэставанне сумяшчальнасціПраверце, ці правільна працуе чып з іншымі кампанентамі або сістэмамі, пераканаўшыся ў адсутнасці няспраўнасцяў або пагаршэння прадукцыйнасці з-за несумяшчальнасці. | Забяспечвае бесперабойную працу ў рэальных праграмах, прадухіляючы праблемы сумяшчальнасці. |
3.3 Упакоўка і захоўванне
Пасля разразання пласцін чыпы з'яўляюцца найважнейшым вынікам працэсу вытворчасці паўправаднікоў, і этапы іх упакоўкі і захоўвання гэтак жа важныя. Правільныя меры па ўпакоўцы і захоўванні неабходныя не толькі для забеспячэння бяспекі і стабільнасці чыпаў падчас транспарціроўкі і захоўвання, але і для забеспячэння надзейнай падтрымкі на наступных этапах вытворчасці, выпрабаванняў і ўпакоўкі.
Кароткі змест этапаў праверкі і выпрабаванняў:
Этапы праверкі і выпрабаванняў мікрасхем пасля разразання пласцін ахопліваюць шэраг аспектаў, у тым ліку візуальны агляд, вымярэнне памераў, праверку электрычных характарыстык, функцыянальныя выпрабаванні, праверку надзейнасці і праверку сумяшчальнасці. Гэтыя этапы ўзаемазвязаны і дапаўняюць адзін аднаго, утвараючы трывалую перашкоду для забеспячэння якасці і надзейнасці прадукцыі. Дзякуючы строгім працэдурам праверкі і выпрабаванняў, патэнцыйныя праблемы можна выявіць і хутка вырашыць, гарантуючы, што канчатковы прадукт адпавядае патрабаванням і чаканням кліентаў.
Аспект | Змест |
Меры па ўпакоўцы | 1.АнтыстатычныУпаковачныя матэрыялы павінны мець выдатныя антыстатычныя ўласцівасці, каб прадухіліць пашкоджанне прылад статычнай электрычнасцю або ўплыў на іх прадукцыйнасць. |
2.ВільгацеўстойлівыУпаковачныя матэрыялы павінны мець добрую вільгацятрываласць, каб прадухіліць карозію і пагаршэнне электрычных характарыстык, выкліканае вільготнасцю. | |
3.УдаратрывалыУпаковачныя матэрыялы павінны забяспечваць эфектыўную амартызацыю, каб абараніць чыпсы ад вібрацыі і ўдараў падчас транспарціроўкі. | |
Асяроддзе захоўвання | 1.Кантроль вільготнасціСтрога кантралюйце вільготнасць у адпаведных межах, каб прадухіліць паглынанне вільгаці і карозію, выкліканую празмернай вільготнасцю, або статычнымі праблемамі, выкліканымі нізкай вільготнасцю. |
2.ЧысціняПадтрымлівайце чысціню ў складскім памяшканні, каб пазбегнуць забруджвання шчэпкі пылам і прымешкамі. | |
3.Кантроль тэмпературыУсталюйце разумны дыяпазон тэмператур і падтрымлівайце стабільнасць тэмпературы, каб прадухіліць паскоранае старэнне з-за празмернага нагрэву або праблем з кандэнсацыяй, выкліканых нізкімі тэмпературамі. | |
Рэгулярная праверка | Рэгулярна правярайце і ацэньвайце захоўваемыя мікрасхемы, выкарыстоўваючы візуальны агляд, вымярэнне памераў і выпрабаванні электрычных характарыстык, каб своечасова выяўляць і вырашаць патэнцыйныя праблемы. Зыходзячы з часу і ўмоў захоўвання, плануйце выкарыстанне мікрасхем, каб забяспечыць іх аптымальны стан. |
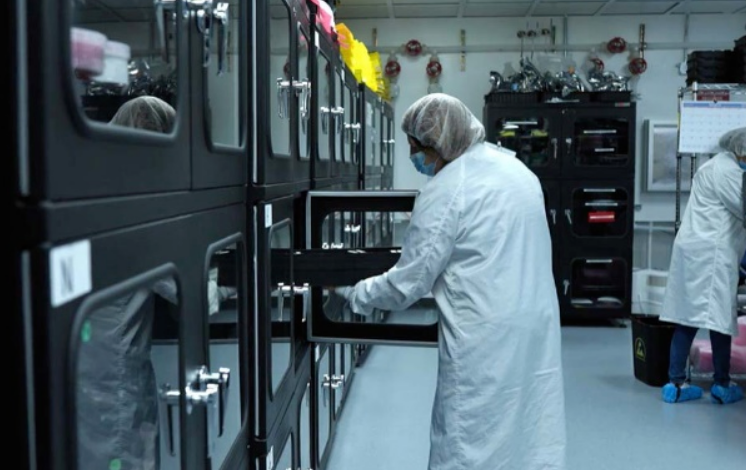
Праблема мікратрэшчыны і пашкоджанняў падчас працэсу нарэзкі пласцін з'яўляецца значнай праблемай у вытворчасці паўправаднікоў. Напружанне рэзання з'яўляецца асноўнай прычынай гэтай з'явы, бо яно стварае дробныя расколіны і пашкоджанні на паверхні пласцін, што прыводзіць да павелічэння вытворчых выдаткаў і зніжэння якасці прадукцыі.
Каб вырашыць гэтую праблему, вельмі важна мінімізаваць напружанне пры рэзцы і ўкараніць аптымізаваныя метады рэзкі, інструменты і ўмовы. Уважлівае стаўленне да такіх фактараў, як матэрыял ляза, хуткасць рэзкі, ціск і метады астуджэння, можа дапамагчы паменшыць утварэнне мікратрэшчыны і палепшыць агульны прыбытак працэсу. Акрамя таго, бягучыя даследаванні больш перадавых тэхналогій рэзкі, такіх як лазерная нарэзка кубікамі, вывучаюць спосабы далейшага вырашэння гэтых праблем.
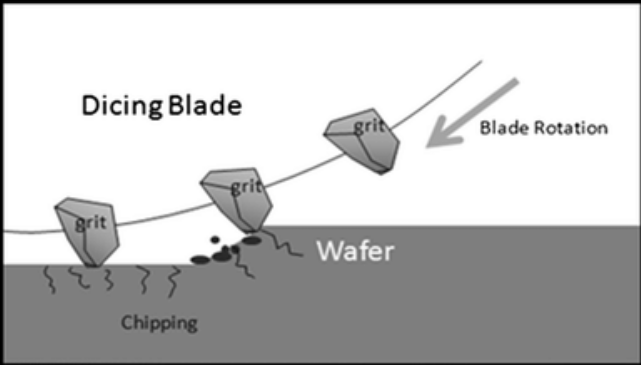
Як далікатны матэрыял, пласціны схільныя да ўнутраных структурных змен пры ўздзеянні механічных, тэрмічных або хімічных нагрузак, што прыводзіць да ўтварэння мікратрэшчыны. Нягледзячы на тое, што гэтыя расколіны могуць быць не адразу прыкметныя, яны могуць пашырацца і прычыняць больш сур'ёзныя пашкоджанні па меры прасоўвання вытворчага працэсу. Гэтая праблема становіцца асабліва праблематычнай на наступных этапах упакоўкі і выпрабаванняў, дзе ваганні тэмпературы і дадатковыя механічныя нагрузкі могуць прывесці да ператварэння гэтых мікратрэшчыны ў бачныя расколіны, што патэнцыйна можа прывесці да паломкі чыпа.
Каб паменшыць гэтую рызыку, важна старанна кантраляваць працэс рэзкі, аптымізуючы такія параметры, як хуткасць рэзкі, ціск і тэмпература. Выкарыстанне менш агрэсіўных метадаў рэзкі, такіх як лазерная нарэзка, можа знізіць механічнае напружанне на пласціне і мінімізаваць утварэнне мікратрэшчыны. Акрамя таго, укараненне перадавых метадаў кантролю, такіх як інфрачырвонае сканаванне або рэнтгенаўская візуалізацыя, падчас працэсу нарэзкі пласціны можа дапамагчы выявіць гэтыя расколіны на ранняй стадыі, перш чым яны прывядуць да далейшай шкоды.
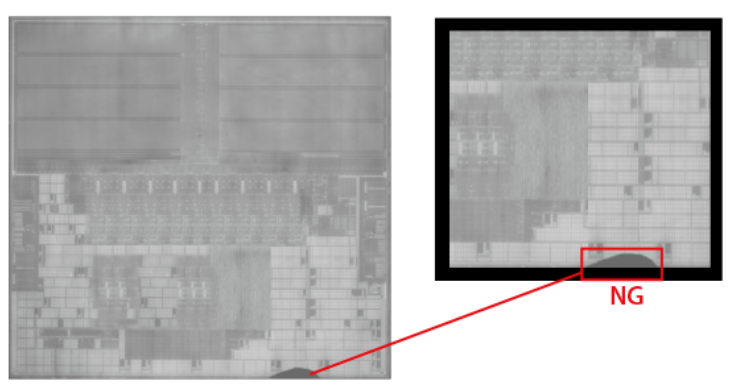
Пашкоджанне паверхні пласціны з'яўляецца сур'ёзнай праблемай у працэсе нарэзкі, бо яно можа непасрэдна паўплываць на прадукцыйнасць і надзейнасць чыпа. Такія пашкоджанні могуць быць выкліканыя няправільным выкарыстаннем рэжучых інструментаў, няправільнымі параметрамі рэзкі або дэфектамі матэрыялу, уласцівымі самой пласціне. Незалежна ад прычыны, гэтыя пашкоджанні могуць прывесці да змяненняў электрычнага супраціву або ёмістасці схемы, што ўплывае на агульную прадукцыйнасць.
Для вырашэння гэтых праблем разглядаюцца дзве ключавыя стратэгіі:
1. Аптымізацыя рэжучых інструментаў і параметраўВыкарыстоўваючы больш вострыя ляза, рэгулюючы хуткасць рэзання і змяняючы глыбіню рэзання, можна мінімізаваць канцэнтрацыю напружання падчас працэсу рэзання, тым самым зніжаючы патэнцыял пашкоджанняў.
2. Вывучэнне новых тэхналогій рэзкіТакія перадавыя тэхналогіі, як лазерная і плазменная рэзка, забяспечваюць павышаную дакладнасць, адначасова патэнцыйна зніжаючы ўзровень пашкоджанняў, якія наносяцца пласціне. Гэтыя тэхналогіі вывучаюцца, каб знайсці спосабы дасягнення высокай дакладнасці рэзкі пры мінімізацыі тэрмічнага і механічнага напружання на пласціну.
Плошча цеплавога ўздзеяння і яе ўплыў на прадукцыйнасць
У працэсах тэрмічнай рэзкі, такіх як лазерная і плазменная рэзка, высокія тэмпературы непазбежна ствараюць зону цеплавога ўздзеяння на паверхні пласціны. Гэтая зона, дзе значны градыент тэмператур, можа змяніць уласцівасці матэрыялу, уплываючы на канчатковыя характарыстыкі чыпа.
Уплыў зоны тэрмічнага ўздзеяння (ЗТЗ):
Змены крышталічнай структурыПры высокіх тэмпературах атамы ў матэрыяле пласціны могуць перабудоўвацца, што прыводзіць да скажэнняў крышталічнай структуры. Гэта скажэнне аслабляе матэрыял, зніжаючы яго механічную трываласць і стабільнасць, што павялічвае рызыку паломкі чыпа падчас выкарыстання.
Змены электрычных уласцівасцейВысокія тэмпературы могуць змяніць канцэнтрацыю і рухомасць носьбітаў зарада ў паўправадніковых матэрыялах, уплываючы на электраправоднасць чыпа і эфектыўнасць перадачы току. Гэтыя змены могуць прывесці да зніжэння прадукцыйнасці чыпа, што патэнцыйна зробіць яго непрыдатным для выкарыстання па прызначэнні.
Каб змякчыць гэтыя наступствы, кантроль тэмпературы падчас рэзкі, аптымізацыя параметраў рэзкі і вывучэнне такіх метадаў, як астуджальныя струмені або пасляапрацоўка, з'яўляюцца важнымі стратэгіямі для зніжэння ступені цеплавога ўздзеяння і захавання цэласнасці матэрыялу.
У цэлым, як мікратрэшчыны, так і зоны цеплавога ўздзеяння з'яўляюцца найважнейшымі праблемамі ў тэхналогіі нарэзкі пласцін. Для паляпшэння якасці паўправадніковай прадукцыі і павышэння яе канкурэнтаздольнасці на рынку неабходныя далейшыя даследаванні, а таксама тэхналагічныя дасягненні і меры кантролю якасці.
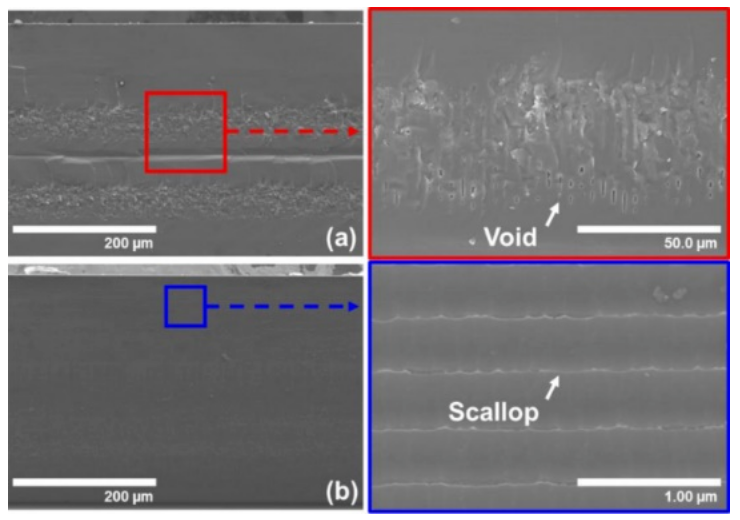
Меры па кантролі зоны цеплавога ўздзеяння:
Аптымізацыя параметраў працэсу рэзанняЗніжэнне хуткасці і магутнасці рэзання можа эфектыўна мінімізаваць памер зоны цеплавога ўздзеяння (ЗЦУ). Гэта дапамагае кантраляваць колькасць цяпла, якое выпрацоўваецца падчас працэсу рэзання, што непасрэдна ўплывае на ўласцівасці матэрыялу пласціны.
Перадавыя тэхналогіі астуджэнняУжыванне такіх тэхналогій, як астуджэнне вадкім азотам і мікрафлюіднае астуджэнне, можа значна абмежаваць дыяпазон зоны цеплавога ўздзеяння. Гэтыя метады астуджэння дапамагаюць больш эфектыўна рассейваць цяпло, тым самым захоўваючы ўласцівасці матэрыялу пласціны і мінімізуючы цеплавыя пашкоджанні.
Выбар матэрыялуДаследчыкі даследуюць новыя матэрыялы, такія як вугляродныя нанатрубкі і графен, якія валодаюць выдатнай цеплаправоднасцю і механічнай трываласцю. Гэтыя матэрыялы могуць паменшыць зону цеплавога ўздзеяння, адначасова паляпшаючы агульную прадукцыйнасць чыпаў.
Карацей кажучы, хоць зона цеплавога ўздзеяння з'яўляецца непазбежным вынікам тэхналогій тэрмічнай рэзкі, яе можна эфектыўна кантраляваць з дапамогай аптымізаваных метадаў апрацоўкі і выбару матэрыялаў. Будучыя даследаванні, верагодна, будуць сканцэнтраваны на тонкай наладцы і аўтаматызацыі працэсаў тэрмічнай рэзкі для дасягнення больш эфектыўнай і дакладнай нарэзкі пласцін.

Стратэгія балансу:
Дасягненне аптымальнага балансу паміж выхадам пласцін і эфектыўнасцю вытворчасці з'яўляецца пастаяннай праблемай у тэхналогіі нарэзкі пласцін. Вытворцам неабходна ўлічваць мноства фактараў, такіх як рыначны попыт, вытворчыя выдаткі і якасць прадукцыі, каб распрацаваць рацыянальную вытворчаю стратэгію і параметры працэсу. У той жа час, укараненне перадавога абсталявання для нарэзкі, павышэнне кваліфікацыі аператараў і ўзмацненне кантролю якасці сыравіны маюць важнае значэнне для падтрымання або нават павышэння выхаду пры адначасовым павышэнні эфектыўнасці вытворчасці.
Будучыя выклікі і магчымасці:
З развіццём паўправадніковых тэхналогій рэзка пласцін сутыкаецца з новымі праблемамі і магчымасцямі. Па меры памяншэння памераў мікрасхем і павелічэння інтэграцыі патрабаванні да дакладнасці і якасці рэзкі значна растуць. Адначасова з гэтым новыя тэхналогіі даюць новыя ідэі для распрацоўкі метадаў рэзкі пласцін. Вытворцы павінны сачыць за дынамікай рынку і тэхналагічнымі тэндэнцыямі, пастаянна карэктуючы і аптымізуючы вытворчыя стратэгіі і параметры працэсу, каб адпавядаць зменам рынку і тэхналагічным патрабаванням.
У заключэнне, інтэгруючы меркаванні рынкавага попыту, вытворчых выдаткаў і якасці прадукцыі, а таксама ўкараняючы перадавое абсталяванне і тэхналогіі, павышаючы кваліфікацыю аператараў і ўзмацняючы кантроль сыравіны, вытворцы могуць дасягнуць найлепшага балансу паміж выхадам пласцін і эфектыўнасцю вытворчасці падчас нарэзкі пласцін, што прывядзе да эфектыўнай і якаснай вытворчасці паўправадніковых вырабаў.
Перспектывы на будучыню:
Дзякуючы хуткаму тэхналагічнаму прагрэсу, паўправадніковыя тэхналогіі развіваюцца беспрэцэдэнтнымі тэмпамі. Як найважнейшы этап у вытворчасці паўправаднікоў, тэхналогія рэзкі пласцін гатовая да новых захапляльных распрацовак. У будучыні чакаецца, што тэхналогія рэзкі пласцін дасягне значных паляпшэнняў у дакладнасці, эфектыўнасці і кошту, што ўнясе новую жыццёвую сілу ў далейшы рост паўправадніковай прамысловасці.
Павышэнне дакладнасці:
У імкненні да больш высокай дакладнасці тэхналогія рэзкі пласцін будзе пастаянна пашыраць межы існуючых працэсаў. Дзякуючы глыбокаму вывучэнню фізічных і хімічных механізмаў працэсу рэзкі і дакладнаму кантролю параметраў рэзкі, будуць дасягнуты больш дакладныя вынікі рэзкі, якія адпавядаюць усё больш складаным патрабаванням да праектавання схем. Акрамя таго, вывучэнне новых матэрыялаў і метадаў рэзкі значна палепшыць выхад і якасць.
Павышэнне эфектыўнасці:
Новае абсталяванне для рэзкі пласцін будзе сканцэнтравана на разумным і аўтаматызаваным праектаванні. Укараненне перадавых сістэм кіравання і алгарытмаў дазволіць абсталяванню аўтаматычна рэгуляваць параметры рэзкі ў адпаведнасці з рознымі матэрыяламі і патрабаваннямі да канструкцыі, тым самым значна павышаючы эфектыўнасць вытворчасці. Такія інавацыі, як тэхналогія шматпласціннай рэзкі і сістэмы хуткай замены лязоў, будуць адыгрываць вырашальную ролю ў павышэнні эфектыўнасці.
Зніжэнне выдаткаў:
Зніжэнне выдаткаў з'яўляецца ключавым напрамкам развіцця тэхналогіі рэзкі пласцін. Па меры распрацоўкі новых матэрыялаў і метадаў рэзкі чакаецца эфектыўны кантроль выдаткаў на абсталяванне і тэхнічнае абслугоўванне. Акрамя таго, аптымізацыя вытворчых працэсаў і зніжэнне ўзроўню браку яшчэ больш скароцяць колькасць адходаў падчас вытворчасці, што прывядзе да зніжэння агульных выдаткаў на вытворчасць.
Разумная вытворчасць і Інтэрнэт рэчаў:
Інтэграцыя тэхналогій разумнай вытворчасці і Інтэрнэту рэчаў (IoT) прынясе трансфармацыйныя змены ў тэхналогію рэзкі пласцін. Дзякуючы ўзаемасувязі і абмену дадзенымі паміж прыладамі, кожны этап вытворчага працэсу можна будзе кантраляваць і аптымізаваць у рэжыме рэальнага часу. Гэта не толькі павышае эфектыўнасць вытворчасці і якасць прадукцыі, але і забяспечвае кампаніям больш дакладнае прагназаванне рынку і падтрымку ў прыняцці рашэнняў.
У будучыні тэхналогія рэзкі пласцін дазволіць значна павысіць дакладнасць, эфектыўнасць і кошт. Гэтыя дасягненні будуць стымуляваць далейшае развіццё паўправадніковай прамысловасці і прынясуць больш тэхналагічных інавацый і зручнасцей для чалавецтва.
Час публікацыі: 19 лістапада 2024 г.